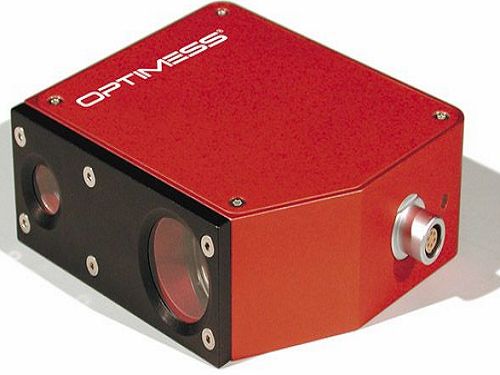
The business intelligence capabilities of the latest generation of sensors are as important as their improved accuracy. "This feature enables end-users to get more product information from the production line, and can also apply this information to optimize the production process." Bob Tremblay, former application engineer and current product sales manager at Cognex, said, "With this information, they may Achieve higher return on investment (ROI).†Cognex is a globally renowned supplier of machine vision and laser displacement sensors.
Although Tremblay did not quantify the potential or real returns, he stated that RIO can be implemented within a few weeks after starting to use the sensor. New applications for other sensors also include production-fine tuning based on sensor intelligence, such as the new laser displacement sensor.
When operating on a rugged surface, the simple measurement and intelligent acquisition functions of the laser displacement sensor can be directly connected, and are generally applied to the automotive and medical equipment industries that need to check the pitting or roughness of the product surface.
Usually flatness is checked offline by a coordinate measuring machine (CMM). “Manufacturers have been tangled up on this issue for a long time,†Tremblay said. “But when we study the small features, such as the height of 0.5 to 1.0 mm (flatness variable), these are difficult to control.â€
Therefore, it takes a lot of time to monitor changes in these characteristics. "If you are lucky, sampling a sample using the CMM can take hours," Tremblay said. Samples of flat products will be moved to the CMM once they come out of the product line, and they will be analyzed after clamping. Then, this process will be reversed. However, due to contact with the product during the process, offline operations may affect the flatness of the surface of the object.
The automatic 3D function of the laser displacement sensor has changed this situation. "The technology ensures non-invasive non-invasive sampling inspection." Tremblay stressed that because the new technology can provide continuous on-line sampling inspection, end-users can always see the sample. If required, any discrepancies within the 5 micron range can be found.
The new sensor technology can also be applied to the electronics industry. In the electronics industry, parts are often transmitted between programs. After transmission is complete, laser displacement sensors can be used to check the corners of a part for wear.
The new technology also applies to measuring parts that are inspected and tested at the same time. Tremblay said, "You may need to measure a device in its application environment, such as a medical device. After the test or test, we can know whether the device has changed."
Severe environment, special needs
Manufacturers with welding operations may need to determine the welding alignment and height. In this harsh environment, Turck's newly improved WeldGuard inductive proximity sensors can be deployed as both a synchronous sensor and a business intelligence device. “Automakers use a large number of sensors on the body, powertrain, subassembly lines and assembly lines.†said Brain Torbox, automotive business development manager for the Turck mobile device market. “The most serious is the welding operation. These sensors are exposed to slag, high temperatures. And physical damage."
The use of sensors in harsh environments means that suppliers like Turck must find new ways to extend the life of the proximity card. "Our sensors are fully adapted to withstand the harsh environment of welding and assembly through modified standard sensors," Torbox said. These improvements include the use of stainless steel or polytetrafluoroethylene (PTFE) cable drums and sleeves during assembly and quick attachment.
Torbox claims that "If a standard sensor can run in a severe welding environment for one day, we can extend its life to one month. Or if the standard sensor can run for a week, we can extend it to six to eight weeks." This indicates Operators and managers of RTF applications do not need to repeatedly deal with downtime due to sensor failure. Instead, they can properly plan and prepare for minimizing production pauses before the sensor card is about to fail.
Torobox estimates based on the end-user data that the loss of each sensor is about $500. These losses were mainly due to the suspension of production. "If the manufacturer fails 50 sensors a day in the entire factory, the accumulated losses will be very heavy."
Preemptive instructions
Frequent production pauses and how to deal with this issue affect the nerves of each manufacturer. "To solve this problem, Sick has improved its existing FX3Flexi soft-mode safety controller to provide more diagnostic and automatic configuration capabilities." Sick security manager SteveAamodt said, "The controller can be used as a company security system The hub provides the logic for the machine."
The new automatic recovery function of the safety controller can help solve this problem from the perspective of fault diagnosis. If the system is down, the time it takes to restart and reinstall the program can be reduced from hours to minutes, and diagnostics can also analyze the cause of the failure.
In many factories, employees find problems by patrolling the workshop looking for flashing red lights. However, with smarter equipment now, this work can be saved directly. For example, if a security scanner captures data from the contaminated production line, the end user can use the robot connected to the scanner to confirm the contaminated electronics and clean it instead of leaving the problem to the end.
This preemptive directive function can be seen as a preventive maintenance capability. Aamodt said, “With sensor prevention capabilities, the more information we provide to the hub, the more employees can make informed decisions based on more information.â€
Aamodt added that if he were a manufacturer seeking new sensor technology to ensure safe operation, he would have four selection criteria. "I would like to adopt a technology that does not affect production, passes safety certifications, does not affect equipment operation, and can provide information on machines and their performance."
Die-Casting Products,Led Die Casting,Pressure Die Casting,Aluminum Die Casting Led
Yangzhou Huadong Can Illuminations Mould Manufactory Co., Ltd. , https://www.light-reflectors.com