First, sound absorption
1.1 Sound absorption coefficient and noise reduction coefficient
Sound absorption is a phenomenon of energy loss after sound waves hit the surface of the material, and sound absorption can reduce the indoor sound pressure level. The indicator describing sound absorption is the sound absorption coefficient a, which represents the ratio of the acoustic energy absorbed by the material to the incident sound energy. In theory, if a material completely reflects the sound, then its a = 0; if a material absorbs all of the incident sound energy, then its a = 1. In fact, a of all materials is between 0 and 1, that is, it is impossible to totally reflect, and it is impossible to absorb them all.
There will be different sound absorption coefficients at different frequencies. The sound absorption coefficient frequency characteristic curve is used to describe the sound absorption performance of the material at different frequencies. According to the ISO standard and the national standard, the frequency range of the sound absorption coefficient in the sound absorption test report is 100-5 KHz. The average value of the sound absorption coefficient of 100-5 KHz is the average sound absorption coefficient, and the average sound absorption coefficient reflects the sound absorption performance of the material as a whole. In the engineering, the noise reduction coefficient NRC is often used to roughly evaluate the sound absorption performance in the language frequency range. This value is the arithmetic mean of the sound absorption coefficients of the materials at the four frequencies of 250, 500, 1K, 2K, rounded to the nearest 0.05. It is generally considered that a material having an NRC of less than 0.2 is a reflective material, and a material having an NRC greater than or equal to 0.2 is considered to be a sound absorbing material. When it is necessary to absorb a large amount of sound energy to reduce indoor reverberation and noise, it is often necessary to use a material with a high sound absorption coefficient. For example, centrifugal glass wool, rock wool and the like are high NRC sound absorbing materials, and the NRC of 5cm thick 24kg/m3 centrifugal glass wool can reach 0.95.
There are two methods for measuring the sound absorption coefficient of a material, one is the reverberation chamber method, and the other is the standing wave tube method. The reverberation chamber method measures the sound absorption coefficient when the sound is randomly incident, that is, the ratio of the energy loss when the sound is injected into the material from all directions, and the standing wave tube method measures the sound absorption coefficient when the sound is normally incident, and the sound incident angle is only 90 degrees. . The sound absorption coefficients measured by the two methods are different. The most commonly used in engineering is the sound absorption coefficient measured by the reverberation chamber method, because the sound incidence is random in the actual application of the building. In some measurement reports, the sound absorption coefficient is greater than 1, which is caused by the laboratory conditions of the measurement. In theory, the sound energy absorbed by any material cannot be greater than the incident sound energy, and the sound absorption coefficient is always less than 1. Any measured sound absorption coefficient value greater than 1 cannot be used greater than 1 in actual acoustic engineering calculations, and may be calculated at a maximum of 1.
In the room, the sound fills the corners quickly, so placing the sound absorbing material on any surface of the room has a sound absorbing effect. The louder the sound absorption coefficient of the sound absorbing material, the more the sound absorption area, the more obvious the sound absorption effect. Acoustic noise reduction can be performed by using sound absorbing ceiling, sound absorbing wall panel, space sound absorbing body, and the like.
1.2 Sound absorption principle
Fiber porous sound absorbing materials, such as centrifugal glass wool, rock wool, mineral wool, plant fiber spraying, etc., the sound absorption mechanism is that there are a large number of tiny connected pores inside the material, along which the sound waves can penetrate into the material and rub against the material. The function converts sound energy into heat. The sound absorbing property of the porous sound absorbing material is that the sound absorption coefficient gradually increases as the frequency increases, which means that the low frequency absorption has no high frequency absorption. The necessary condition for sound absorption of porous materials is that the material has a large number of voids, and the voids communicate with each other, and the pores penetrate into the interior of the material. One of the misconceptions is that a material with a rough surface has sound absorbing properties. Actually, for example, a brushed cement or a surface convex or concave stone has substantially no sound absorbing ability. The second misunderstanding is that materials with a large number of holes inside the material, such as polyphenylene, polyethylene, closed-cell polyurethane, etc., have good sound absorption properties. In fact, these materials cannot penetrate due to the lack of connectivity of internal pores. The internal vibration of the material is frictional, so the sound absorption coefficient is small.
A perforated plate with an air layer on the wall or ceiling, even if the material itself has poor sound absorption properties, this structure also has sound absorbing properties, such as perforated gypsum board, wood board, metal plate, and even slit sound absorbing brick. This type of sound absorption is called Helmholtz resonance sound absorption. The sound absorption principle is similar to the acoustic resonance of a thermos bottle. The external space of the material is connected to the internal cavity through a narrow bottleneck. When the sound wave is incident, at the resonance frequency, the neck is The intense resonance between the air and the internal space consumes acoustic energy. Helmholtz resonance absorption is characterized by a large sound absorption coefficient only at the resonance frequency.
The film or sheet can also absorb sound when there is a cavity in the wall or the ceiling, such as a wooden board, a ceiling made of a metal sheet or a wall panel, etc. The sound absorbing mechanism of this structure is a thin plate resonance sound absorption. At the resonance frequency, the acoustic energy is largely absorbed due to the severe vibration of the thin plate. Thin plate resonance absorption mostly has good sound absorption performance at low frequencies.
Second, sound absorption materials and sound absorption structure
2.1 Centrifugal glass wool
The inner fiber of the centrifugal glass wool is fluffy and interlaced, and there are a lot of tiny pores. It is a typical porous sound absorbing material and has good sound absorption characteristics. Centrifugal glass wool can be made into wallboard, ceiling, space sound absorber, etc. It can absorb the sound energy in the room in a large amount, reduce the reverberation time and reduce the indoor noise.
The sound absorption characteristics of centrifugal glass wool are not only related to thickness and bulk density, but also related to factors such as cover material and structural structure. In the construction application, it is also necessary to take into consideration various aspects such as cost, beauty, fire prevention, moisture resistance, dust, and aging resistance.
Centrifugal glass wool is a porous sound absorbing material with good sound absorption properties. The reason why centrifugal glass wool can absorb sound is not because of the rough surface, but because of the large number of tiny pores and pores that communicate inside and outside. When sound waves are incident on the centrifugal glass wool, sound waves can enter the inside of the material along the pores, causing vibration of air molecules in the gap. Due to the viscous resistance of the air and the friction between the air molecules and the pore walls, the acoustic energy is converted into heat energy and lost. Welcome to Home Theater Network
Centrifugal glass wool has good sound absorption performance for high frequency in sound. The main factors affecting the sound absorption performance of centrifugal glass wool are thickness, density and air flow resistance. Density is the weight of material per cubic meter. The air flow resistance is the ratio of the air pressure to the air flow rate on both sides of the material per unit thickness. Air flow resistance is the most important factor affecting the sound absorption performance of centrifugal glass wool. The flow resistance is too small, indicating that the material is sparse, the air vibration is easy to pass through, and the sound absorption performance is degraded; the flow resistance is too large, indicating that the material is dense, the air vibration is difficult to be introduced, and the sound absorption performance is also lowered. For centrifugal glass wool, the sound absorption performance has the best flow resistance. In actual engineering, it is difficult to measure the air flow resistance, but it can be roughly estimated and controlled by thickness and bulk density. 1. As the thickness increases, the mid-low frequency sound absorption coefficient increases remarkably, but the high frequency does not change much (high-frequency absorption is always large). 2. The thickness is constant, the bulk density increases, and the sound absorption coefficient of the middle and low frequency also increases; but when the bulk density increases to a certain extent, the material becomes dense, the flow resistance is greater than the optimal flow resistance, and the sound absorption coefficient decreases. For centrifugal glass wool with a bulk density of more than 5 cm and a bulk density of 16 kg/m3, the low frequency 125 Hz is about 0.2, and the sound absorption coefficient of medium and high frequency (>500 Hz) is already close to one. When the thickness continues to increase from 5 cm, the sound absorption coefficient of the low frequency gradually increases. When the thickness is more than 1 m, the sound absorption coefficient of the low frequency 125 Hz will also be close to 1. When the thickness is constant and the bulk density is increased, the low-frequency sound absorption coefficient of the centrifugal glass wool will also increase continuously. When the bulk density is close to 110kg/m3, the sound absorption performance reaches the maximum value, 50mm thick and the frequency is close to 0.6-0.7 at 125Hz. When the bulk density exceeds 120kg/m3, the sound absorption performance decreases, because the material becomes dense, and the mid-high frequency sound absorption performance is greatly affected. When the bulk density exceeds 300kg/m3, the sound absorption performance is greatly reduced. The thickness of sound-absorbing glass wool commonly used in architectural acoustics is 2.5cm, 5cm, 10cm, and the bulk density is 16, 24, 32, 48, 80, 96, 112kg/m3. Centrifugal glass wool of 5 cm thick and 12-48 kg/m3 is usually used.
The sound absorption performance of centrifugal glass wool is also closely related to the installation conditions. When there is an air layer behind the glass wool board, the sound absorption effect of the glass wool board having the same thickness and no air layer is similar. In particular, the sound absorption performance of the middle and low frequency is much higher than that of the material on the hard bottom surface, and the sound absorption coefficient will increase as the thickness of the air layer increases, but the effect is not obvious after increasing to a certain value.
The use of glass wool stacks of different bulk densities together to form a form of increasing bulk density allows for greater sound absorption. For example, a sound absorption effect of a 2.5 cm thick 24 kg/m3 cotton board and a 2.5 cm thick 32 kg/m3 cotton board is better than a 5 cm thick 32 kg/m3 cotton board. The 24kg/m3 glass wool board is made into a 1m-long triangular tip, and the material density increases gradually, and the average sound absorption coefficient can be close to 1.
In the construction of centrifugal glass wool, the surface is often attached with a certain sound-permeable finish, such as plastic film less than 0.5mm, metal mesh, window screen, fireproof cloth, glass cloth, etc., can basically maintain the original sound absorption characteristics. Centrifugal glass wool has excellent properties such as fireproofing, heat preservation and easy cutting. It is one of the most commonly used materials for building sound absorption. However, since the surface of the centrifugal glass wool is not decorative, and there is a fiber sprinkling, it is necessary to make various sound absorbing members concealed. The most commonly used and lowest cost construction is the ceiling of a perforated gypsum board or a perforated panel wall filled with centrifugal glass wool. When the perforation rate is greater than 20%, the sound absorption performance of the centrifugal glass wool can be fully utilized. . In order to prevent the glass wool fiber from spilling out, it is necessary to attach a layer of a sound-permeable fabric such as a non-woven fabric or a mulberry paper to the back of the perforated plate, or to wrap the glass wool with a glass cloth, a plastic film or the like. Panels similar to perforated gypsum board are perforated metal sheets (such as aluminum sheets), perforated boards, perforated fiber cement boards, perforated mineral wool boards, and the like.
The glass wool board can be processed into a sound absorbing ceiling board or a sound absorbing wall board. Generally, 80-120kg/m3 glass wool board is cured by glue curing, and the fire-proof sound-permeable fabric is formed to form a sound-absorbing wall board which is both beautiful and convenient to install. The common size is 1.2m×1.2m, 1.2m×0.6m, 0.6 m × 0.6 m, thickness 2.5 cm or 5 cm. There is also a sound absorbing ceiling plate formed by directly spraying a sound-permeable decorative material on the surface of the glass wool of 110 Kg/m3. Whether it is a glass wool sound absorbing wall panel or a sound absorbing ceiling panel, it is necessary to use a high bulk glass wool and a certain strengthening treatment to prevent the sheet from being deformed or too soft. This type of building material has good decorative properties and retains the good sound absorption characteristics of centrifugal glass wool. The noise reduction coefficient NRC can generally reach above 0.85. [page]
In a large space such as a gymnasium or a workshop, in order to absorb noise and reduce noise, a sound absorbing body using centrifugal glass wool as a main sound absorbing material is often used. The sound absorbing body can be made into a plate shape, a column shape, a cone or other shaped body as required. The sound absorbing body is filled with centrifugal glass wool, and the surface is wrapped with a sound-permeable surface layer. Since the sound absorbing body has a plurality of surface sound absorbing sounds, the sound absorbing efficiency is high.
In the road sound insulation barrier, in order to prevent noise reflection, it is necessary to take sound absorption measures on the side facing the vehicle, and often also use centrifugal glass wool as a filling material and a barrier plate whose surface layer is a perforated metal plate. In order to prevent the glass wool from absorbing water and moisture outside, it is sometimes wrapped with PVC or plastic film.
2.2 paper perforated gypsum board
Paper perforated plasterboard is often used for building decoration sound absorption. The gypsum board itself does not have good sound absorption performance, but after being perforated and installed as a ceiling or veneer wall with a certain back cavity, a "Helmholtz resonance" sound absorbing structure can be formed, thus obtaining a larger Sound absorption ability. This paper perforated sound absorbing structure is widely used in acoustic engineering such as hall sound quality and sound absorption and noise reduction.
After the gypsum board is perforated, the small hole on the gypsum board forms a resonance cavity with the gypsum board itself and the surface layer of the original building structure. After the sound and the perforated gypsum board act, the air column at the round hole generates a strong resonance, and the air molecules It rubs strongly against the wall of the gypsum board, so that the sound energy is consumed in a large amount, and sound absorption is performed. This is the basic principle of the "Helmholtz resonance" sound absorption of the perforated plasterboard. The sound absorption of the perforated gypsum board has certain selectivity to the sound frequency, and the sound absorption frequency characteristic curve is mountain-shaped. When the sound frequency is close to the resonance frequency, the sound absorption coefficient is large; when the sound frequency is far away from the resonance frequency, the sound absorption coefficient is small. . If the paper perforated gypsum board is covered with a layer of mulberry paper or thin sound-absorbing felt, the frictional resistance of air molecules during resonance increases, and the sound absorption performance of each frequency will be significantly improved. This is why people often use perforated paper. A layer of mulberry paper or a thin sound-absorbing felt is added to the surface of the plasterboard to increase the sound absorption. Welcome to Home Theater Network
The main factors affecting the sound absorption performance of the paper perforated gypsum board are the perforation rate and the size of the back cavity. The perforation aperture and the thickness of the gypsum board have little effect on the sound absorption performance. When the perforation rate increases gradually from 2% to 15%, the surface area occupied by the pores increases, the probability of air molecules entering the resonance cavity participating in the resonance increases, and the sound absorption capacity increases, if the sound absorbing material is placed in the rear cavity. The sound absorption is stronger. The perforation rate affects the resonance frequency, the perforation rate increases, and the resonance frequency shifts to the high frequency, and the offset is proportional to the opening number of the perforation rate. As the perforation rate increases, the “mountain peak†of the sound absorption frequency characteristic curve will move to the right side (high frequency), and the “mountain peak†shape tends to rise as a whole, and the average sound absorption coefficient increases. Increasing the perforation rate can improve the sound absorption performance, but the perforation rate is generally in the range of 2% to 15% due to the limitation of the strength of the gypsum board.
When the rear cavity is increased, the number of air molecules in the resonant cavity increases, and the number of air molecules participating in the consumption of acoustic energy increases during resonance, and the sound absorption performance increases. Changing the size of the cavity is a common method of adjusting the sound absorption coefficient of the perforated gypsum board. The size of the back cavity will affect the resonant frequency, the cavity will increase, the resonant frequency will shift to the low frequency, and the offset will be inversely proportional to the opening number of the cavity depth. The “mountain†of the sound absorption frequency characteristic curve will be left (low frequency). ) Moving, the "mountain peak" pattern tends to rise as a whole, and the average sound absorption coefficient becomes larger. However, when the cavity depth is too large, the "air spring" effect in the cavity is weakened, and the sound absorption performance is lowered. Generally, the cavity depth is preferably within 5-50 cm.
In the usual range, the perforation aperture size is generally 3-10mm, and the gypsum board thickness is generally 9.5mm, 12mm or 15mm. These factors affect the resonance frequency more and more, and the influence on the average sound absorption performance of the perforated gypsum board is very high. small. As the aperture increases or the thickness increases, the resonant frequency will shift to the low frequency, and the offset is inversely proportional to the opening number of the aperture or thickness. The “mountain†of the sound absorption frequency characteristic curve will move to the left (low frequency), and the “mountain peak†form It remains basically unchanged, so the average sound absorption coefficient is basically unchanged. According to the experiment, the change of the aperture size or the thickness of the gypsum board, the average sound absorption coefficient has basically no major change, generally within 10%, and the change of the resonance frequency is only in the range of one to two 1/3 octave. In the actual project of noise reduction, the selection of the aperture and thickness is mainly determined according to the required strength of the application. The aperture selection is 3-10mm, and the thickness of the plate is 9-15mm. Different thickness or aperture can be neglected. Impact.
2.3 Other commonly used sound absorbing materials
Porous fiber sound absorbing materials similar to centrifugal glass wool include rock wool, mineral wool board, open-cell poly-flame-retardant ammonia grease, cellulose spray, and sound-absorbing curtain. Rockwool is made by melting basalt after melting. The diameter of the fiber is generally about 10μ. The centrifugal glass wool is formed by melting the glass after melting, and the fiber diameter is finer, generally below 6μ. Therefore, the bulk density of rock wool is often larger than that of centrifugal glass wool. The sound absorption performance of rock wool is close to that of centrifugal glass wool. The 5cm thick rock wool with a bulk density of 80kg/m3 is equivalent to the sound absorption performance of centrifugal glass wool of 24kg/m3, and the NRC is about 0.95. The mineral wool board is formed by melting and blowing the blast furnace slag to form a fiber, which is then dried to form a sheet. The thickness is generally 12-18 mm, and the NRC is 0.3-0.4, which is often used as a ceiling ceiling. Flame-retardant polyurethane is a kind of soft foam material. It is divided into open-hole and closed-cell. The open-celled cells are connected to each other. The elasticity is good and the sound absorption performance is good. It is often used in the theater sound-absorbing seat liner. Or sound insulation cover lining, NRC is about 0.5-0.6 when 50cm thick and 40kg/m3; closed-cell type closed, no sound absorption, often used for heat preservation or waterproof sealing materials. Cellulose spray material is made by mixing fiber sound absorbing material with water and glue and spraying on ceiling or wall. It is easy to construct and is suitable for construction of complex or surface complex engineering. Representative material is K13 on hard wall. Spraying 2.5 cm thick K13, NRC can reach 0.75. Heavy-duty, wrinkled, fire-resistant curtains are also commonly used for building sound absorption, as curtains are easy to pull open and close, and are often used for variable sound absorption. The rock wool or glass wool can be made into a sharp shape of about 1 m long to form a strong sound absorbing structure. The sound absorption coefficient of each frequency can reach 0.99, which is the structure with the strongest sound absorption performance, and is often used in the sound elimination laboratory or workshop. Sound absorption and noise reduction.
The perforated resonant sound absorbing structure similar to the perforated gypsum board also has a cement perforated plate, a wood perforated plate, a metal perforated plate, and the like. The sound absorption performance of cement and wood perforated board is close to the perforated gypsum board. The cement perforated board is low in cost, but the decoration is poor. It is often used in the sound absorption of machine room and basement. The wood perforated board is beautiful and decorative, but it is fireproof and waterproof. Poor, high price, often used in the hall to absorb sound decoration. Metal perforated plates are commonly used as sound-absorbing ceilings or sound-absorbing walls. The perforation rate can be as high as 35%, and the back space is more than 20cm. The glass wool and rock wool are filled inside, and the NRC can reach 0.99. Applying a layer of sound absorbing paper or sound absorbing felt after the perforated plate can improve the resonance friction efficiency of the hole and greatly improve the sound absorbing performance. Micropores having a diameter of less than 1.0 mm are formed on a thin metal plate having a plate thickness of less than 1 mm to form a microperforated sound absorbing plate. The micro-perforated plate has a higher sound absorption coefficient than the ordinary perforated plate, and the sound absorption frequency band is generally 1% to 2%, and the rear part does not need to be lined with the porous sound absorbing material.
Third, the calculation of sound absorption and noise reduction effect
3.1 Calculation of sound absorption and noise reduction Sound absorption and noise reduction reduce the sound energy of reflected sound. If the influence of direct sound is ignored, the sound absorption is increased by 1 time and the noise is reduced by 3dB. The calculation formula is:
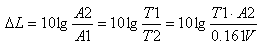
Where ΔL is the amount of noise reduction, and A1, T1, and A2, T2 are the room sound absorption and reverberation time before and after the sound absorbing material is added, and V is the room volume.
If the room is not treated with sound absorption, the reflection is more serious, the sound absorption is less, and the reverberation time is longer, then the sound absorption and noise reduction effect is better. If the original room already has a large amount of sound absorption and the reverberation time is short, the sound absorption effect is relatively poor.
Example: The volume of a room is V=400m3, the reverberation time is 6s, and the sound absorption coefficient of 0.9m is added to the sound absorption ceiling of 100m2. What is the noise reduction? According to the noise reduction formula, ΔL = 10 lg [8 × 90 ÷ (0.161 × 400)] = 9.2 dB.
3.2 Influence of indoor sound source on sound absorption and noise reduction
If there are multiple sound sources in the room, the direct sounds everywhere are strong, and the sound absorption effect is relatively poor, often only 3-4dB. Although the amount of reduction is limited, the reverberation is reduced, and the indoor staff's subjectively eliminates the confusion of noise from all directions, which is better reflected. The sound absorption treatment has a poor effect on the position where the sound source is close to the distance, and has a good effect on the position where the sound source is far away, and the noise reduction effect transmitted to the outside is also obvious.
3.3 Sound absorption and noise reduction effect is related to room shape, size and sound absorption position
If the room volume is large, people's active area is close to the sound source, and the direct sound dominates, and the sound absorption effect is poor. In a room with a small volume, the sound is reflected on the ceiling and the wall for a number of times, and then mixed with the direct sound, and the sound is reflected. At this time, the sound absorption effect is obvious. Experience has shown that the noise reduction effect of the room below 3000m3 is good, the larger room, the sound absorption effect is not ideal. However, if the room is long and thin, the ceiling is low, and the length of the room is more than 5 times of the height and width. Because the sound reflection is similar to crawling in the pipeline, the noise reduction effect of the sound absorption treatment is also better.
3.4 The spectral characteristics of the sound absorbing material should be adapted to the spectral characteristics of the noise source.
The sound absorbing material should be selected for the spectral characteristics of the sound source, and the spectrum of the sound absorbing material should match the spectral characteristics of the noise source. High-frequency noise is mostly made of high-frequency sound-absorbing materials, and low-frequency noise is used by low-frequency sound-absorbing materials. If a perforated resonant sound absorbing material is used, it is preferable to make the peak of the sound absorption frequency correspond to the maximum value of the noise frequency. If the noise has a peak at the medium and high frequency, the noise reduction effect of the processing is very significant.
3.5 Architectural application considerations
When applied in buildings, the sound absorption performance of sound absorbing materials and sound absorbing structures should be stable, fireproof, durable, non-toxic, moderately priced, convenient for construction, no secondary pollution, beautiful and practical.
The stepping motor is an induction motor. Its working principle is to use electronic circuit to supply power when the DC power is changed into components. The multi-phase timing control current is used to supply the stepping motor with this current, and the stepping motor can work normally. The driver is the time-division power supply for the Stepper Motor, multi-phase timing controller.
Step motor,Stepper motor,Small stepper motor,Micro stepper motor,Geared stepper motor,High torque stepper motor
Shenzhen Maintex Intelligent Control Co., Ltd. , https://www.maintexmotor.com